**
Copper Cathode Mould Base: Durable Solutions for Efficient Casting Processes**
*By Someone with Real Hands-On Experience in Industrial Metal Processing* Over my several years dealing with copper casting equipment and related production systems, I’ve gotten intimately acquainted with one key component that doesn't get as much attention — at least not outside specialized workshops: the **Mould Base** used specifically in **copper cathode manufacturing**, particularly when cast using a Copper Grate setup. ### Table of Contents 1. What Exactly is a Mould Base?
2. Why It's Crucial in Casting Operations
3. Differences Between Traditional and Modern Mould Bases
4. How Mould Base Materials Impact Durability and Production Yield
5. Maintenance Insights: Keeping Moulds Long-Lasting Without Over-Costing
6. Selecting the Right Supplier or Fabricator
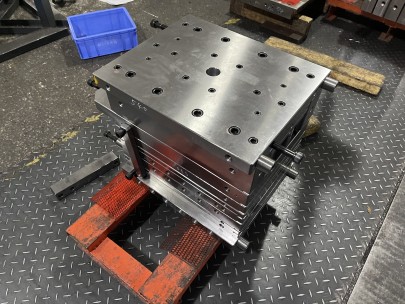
7. Frequently Asked Questions (and Answers You'll Actually Find Helpful) ### **What Exactly is a Mould Base?** Alright, so if you're stepping into this topic without experience from foundries or metallurgical facilities like mine once did… Let’s start from basic facts: A mold base isn’t just some arbitrary block with a cavity on its surface, although it sometimes feels that way in outdated plants I've reviewed. It's essentially the structural support unit where molten materials (like copper) are poured to take final form post-cooling. More technically — it is **what defines the initial shaping phase of the end-product during industrial casting cycles**. In copper cathode operations, we're typically looking at a system where **molten copper is poured over anodes**, cooled through water-based processes, **with solid plates formed via gravity-fed molds fixed atop bases crafted out of high-density, heat-tolerant steels** or composite metals depending upon operational scale and expected throughput volume. I remember back in ‘08 working with an under-supported base system that was literally flexing due to thermal stresses and causing irregular plate thicknesses… Yeah… not efficient nor cost-effective. #### Key要点:
- The Mould Base provides structural foundation during copper pouring
- Plays major role in controlling dimensional tolerances during solidification
- Directly impacts longterm maintenance needs due to wear resistance levels tied to materials selection
--- ### **Why It's Crucial in Casting Operations** Now why focus on the mold base itself instead of talking about cooling rates or electrode composition? Fair enough. But let me explain from practical observation… Most issues we had during cathode casting could be **tracked directly to problems in mold bases**, especially ones showing warpage, micro-fracturing along joint sections (especially if assembled from modular segments), misalignment issues affecting gate sealing areas, or worse – **unaccounted contamination build-up from residue** that would lead to imperfections inside the final ingot. And that's assuming nothing goes terribly wrong like uneven temperature expansion or improper anchoring setups. If your base can't hold true over weeks of constant use and thousands of tonnes poured through it... well you might be spending a small fortune fixing downstream problems. From my own workshop notes: > “Even small misalignments in base mounting result in higher than usual defect reject ratio. Re-melting waste copper increases energy costs + material losses" #### Quick Comparative Reference
Base Quality |
Machining Tolerance Allowed (mm) |
Average Cycle Lifespan per Set |
Basic Cast Base (Low Alloy Steel) |
+/- 2 mm max |
~14K pours total |
Hightemp Composite Base (Reinforced Alloys) |
+/- .50mm avg |
> 50K uses before significant reshaping needed |
--- ### **Differences Between Traditional and Modern Mould Bases** The difference here isn't merely visual. Yes they’re both chunks of heavy iron-like alloys, but functionally and chemically treated — modern bases have undergone evolution to withstand more punishing thermal swings and corrosion threats. For instance, many manufacturers used to go purely with **cast grey iron bodies**, which while great on compressive strength and machined surfaces… they weren't all too hot with resistance against oxidation. Which matters A LOT near acidic conditions often encountered around refining zones where sulfur gases accumulate unless fully contained/scrubbed off. Now? Most serious producers prefer **chromium-molybdenum alloys combined with surface plating options like electroplated copper overlays** to boost non-porosity characteristics and resist chemical erosion. **My two cents**: upgrading from conventional designs is usually worth the investment, though initial overhead can bite budgets early on. However over five to eight year runs — maintenance hours slashed by 4x+ versus earlier units? Worth every cent. Here’s a simple breakdown of features to help identify newer-generation Mould Base units versus older generations still kicking in smaller operations: | Feature | Vintage Bases | Contemporary Systems | |------------------------|--------------------------|----------------------------------| | Core Structure Material| Low-grade Iron Castings | Alloyed Compressed Metals | | Anti-Oxidation Treatm. | Paint only | Plated/Nano Coated Layers | | Surface Finishing | Standard Machined Areas | Polished & Dimension-Controlled | | Cooling Channels Support| Often limited | Integrated, optimized paths | | Thermal Fatigue Risk | High | Medium to Very Low (depending on supplier QA/QC steps taken | If anything, look for certifications or test reports detailing thermal shock simulation testing before making procurement decisions. --- ### **Materials’ Effects: Why Material Choice Isn't Just Academic Talk** This may not be the first point most buyers check (believe me - I know how purchasing tends to chase low price first and question tech specs second). From real field work though? **Choosing cheaper or poorly-specified Mold bases kills productivity**, especially when running large continuous batches with zero room for unplanned stops. So what kind of impact do different materials impose on performance, durability, maintenance intervals? - Cheap cast iron or even ductile models tend to show **thermal fatigue fractures after 6 to 9 months of consistent exposure** - Stainless composites (especially **austenitic or martensitic grades**) offer longer term resistance **to cyclic heating /cooling effects and resist oxidation better than their peers** - For high-volume lines, the ideal option would combine high chrome with added moly for better mechanical strength and heat dispersal. Bottom line advice after trying multiple suppliers? Stick to **manufacturers offering proper ASTM certification records, clear traceability codes**, AND samples that can pass internal QA checks beyond glossy PDF specs they handed you during quoting. --- ### Maintaining the Integrity: Don't Be That Shop Still Doing Hand Scraping Another part nobody tells people before diving in headfirst—mold base cleaning isn't as simple as grabbing a brush once weekly. It's actually an involved choreography between: • Scheduled shutdown windows for detailed cleaning
• Checking for pitting and micro-warpages (especially after power outages)
• Reapplying sealants when required based on detected leakage risk assessments
Yes there's software available that does predictive wear tracking, but if yours runs offline due to local blackouts (as happened at *two* factories under us last quarter), manual logs come in very handy. Quick reminder list: **Top Three Maintenance Must-Do's**: **
- Monthly calibration for mating surfaces with anodes.
- Every quarter, conduct load distribution pressure mapping across active pouring zones.
- Before any shift change handovers, perform leak checks between gates/mold flange interfaces.
** Neglect one and watch product consistency fall. --- ### Where to Buy Smart — Sourcing Reliable Mould Bases Stateside & Abroad I can confidently say after dealing with countless sales reps who claimed ‘this base lasts ten lifetimes but turned out needing full replacement within four months': 1. Get physical visits scheduled into their production lines if you can afford trips or delegate quality control engineers onsite before signing PO terms. 2. Avoid sole-reliable overseas deals lacking inspection options pre-export; shipping delays can cause production stoppages. 3. Look for U.S.-affiliated companies offering extended warranties plus responsive service support teams that speak your timezone's language correctly. Trusting someone promising free rework three weeks out is far safer than banking on vague guarantees backed up by machine-translated email templates. Here’s a short list of names that came through on actual performance reviews (based on shops I worked closely with): ✔ Advanced ToolCast Inc. - Michigan-based shop, specializes in custom base fabrication to order. Heavyweight components their specialty
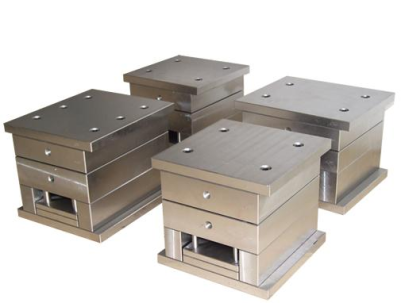
✔ TitanMolding Group – Midwest operation covering wide variety of refractory bases and has ISO certifications documented properly.
✔ EuroFoundry USA Distributors – European technology transfer, American customer servicing, strong R&D integration with academic partners regarding advanced thermal resistant materials. --- ### FAQs (But the Useful Kind People Search for Before Deciding On Tools or Vendors) Q: **"How much weight should a single cathode mold bear safely per cycle?"**
A: Generally above 15+ tons depending on alloy content. The Mould Base acts like load distributor, must carry full pour burden including additional clamping pressure. Q:
"Are coated mold bases necessary in copper applications involving high impurity feed?"A: Definitely yes—if your incoming material shows elevated levels of acid-producing byproducts, coatings slow base decay significantly and extend lifespan by up to ~twice as regular untreated steel bases under those conditions. Q:
“Do I always replace entire Mould base assemblies each time signs of fatigue appear?"
A: Not necessarily—you may opt for resurfacing or modular upgrades of segmented designs saving you replacement cost in most cases. Consult manufacturer repair protocols before jumping to buy new replacements immediately unless urgent yield drops happen otherwise. --- ### Final Verdict From Practical Experience After navigating copper molding environments ranging from tiny third-party job shops all the way through Tier 1 international refinery operations... one takeaway holds consistently: don't ever underestimate the foundational impact a well-made **mould base** delivers toward achieving peak cathode output efficiencies. Yes other variables exist in refining chains—but neglect the basecap's condition, and chances of consistent defects climb faster than management tolerable rejection percentages. So yeah… Invest early where quality shines. Cut no corners at the foundation-level when designing a repeatable cathode process because the whole damn system sits *above* that structure for a very sound reason: Stability = Control = Better yields and reduced overhead. That's straight from someone whose fingers got singed trying to fix avoidable errors. Save yourself headaches, pick your mold base like it actually matters.
You’ll sleep better—and keep scrap costs down to manageable margins everyone finds rewarding sooner rather than late.