
Job: unknown
Introduction: No Data
The Ultimate Guide to Choosing the Perfect Copper Plate for Your Die Base Needs
Die base
Publish Time: Jun 15, 2025
The Ultimate Guide to Choosing the Perfect Copper Plate for Your Die Base Needs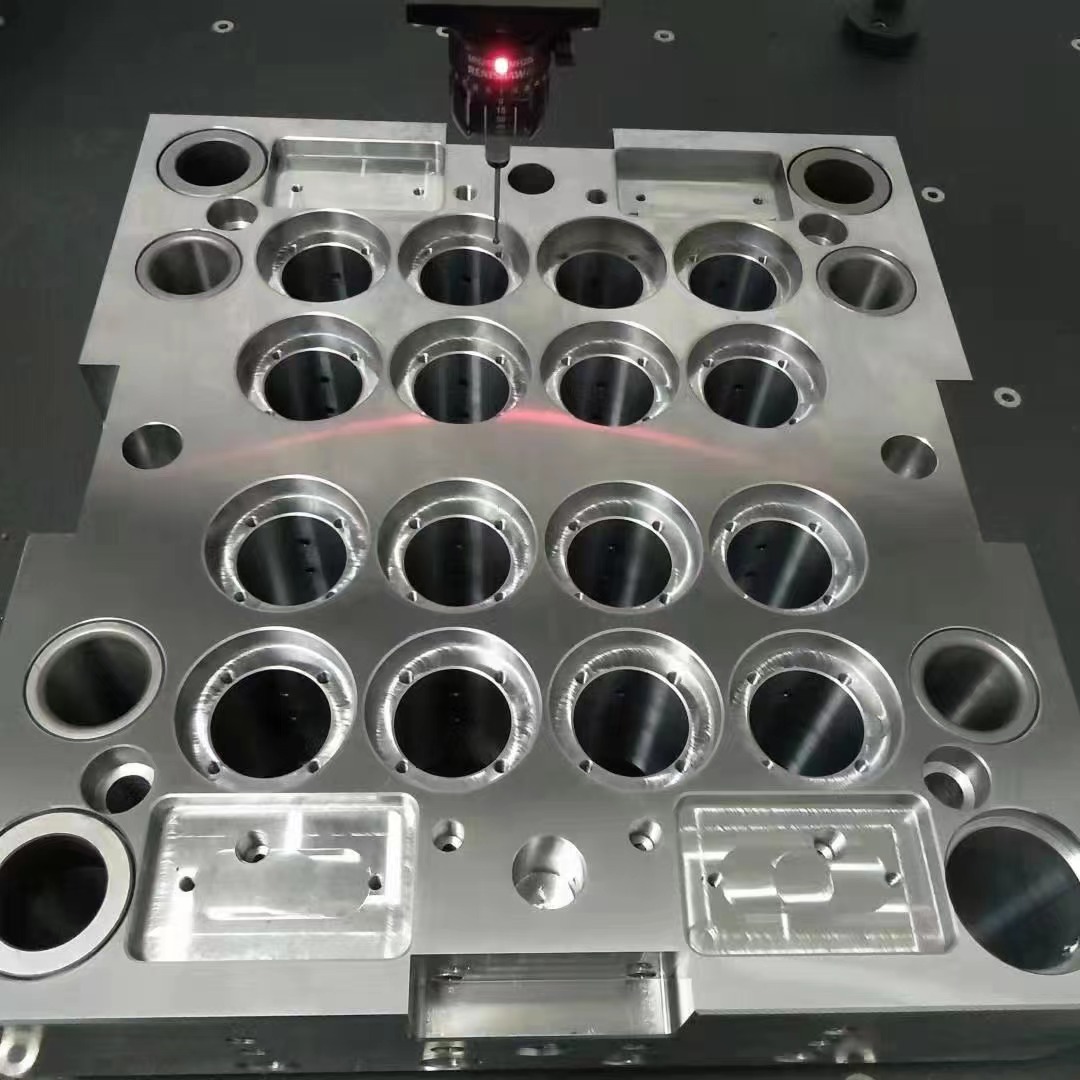
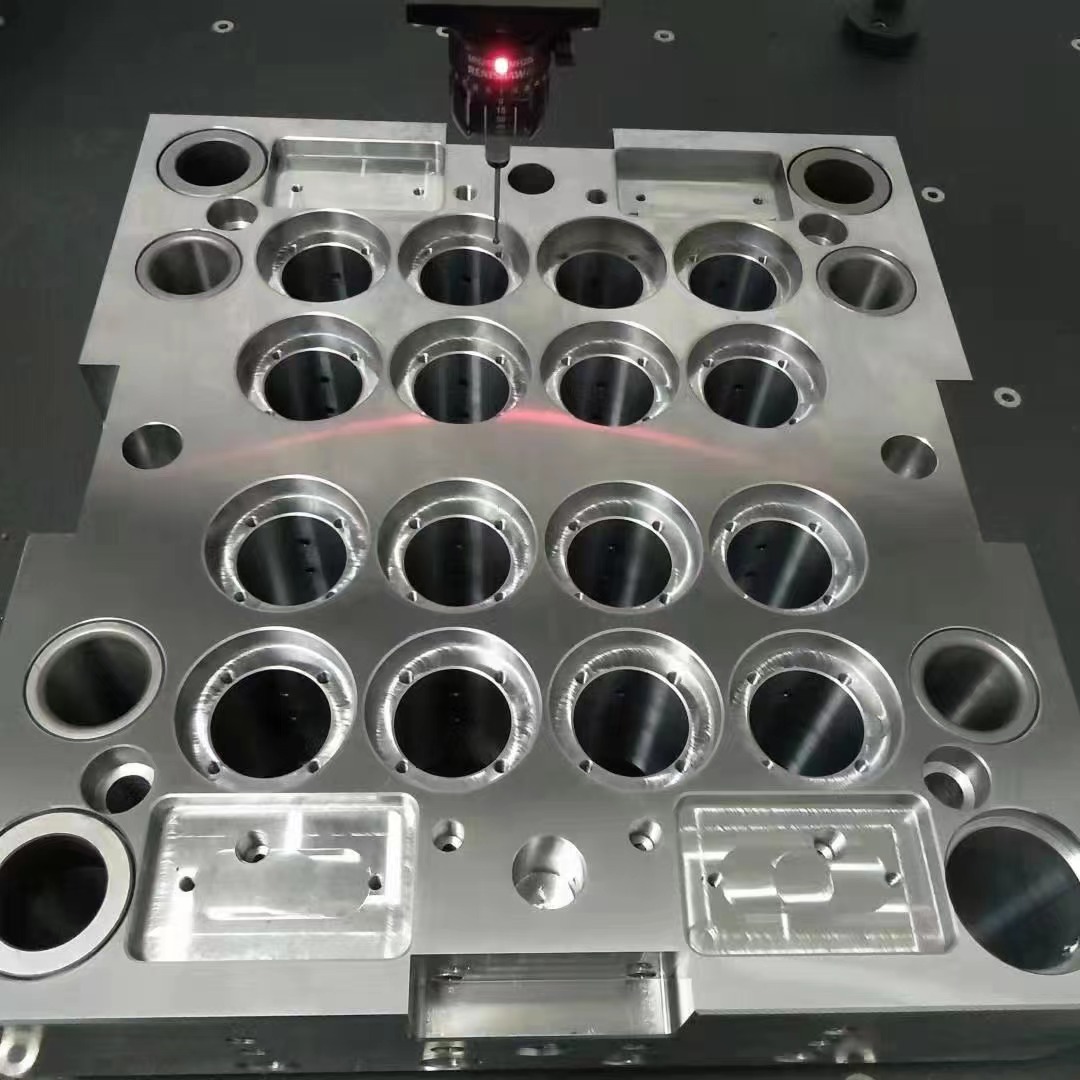
**标题:** The Ultimate Guide to Choosing the Perfect Copper Plate for Your Die Base Needs Alright, lets dive into somethin' I’ve spent a good deal of time figurin’ out — pickin' the right copper plate for your die base needs. It ain’t somethin’ u can skip or just "make do". The type of **copper plate** u use could literally make or break the outcome of the die casting game. First things first: if u haven't already heard about what is **base cap moulding** used for—well, this guide's gonna clear that up, too. So hold yer hat tight, 'cause I got some solid intel from real-world applications n experiments with **Die Base** systems that'll help u navigate this sometimes tricky domain known as **Cooper Menu**, which honestly, isn’t even about lunch options 😅 --- ### What Exactly is a Die Base and Why Does It Matter Anyway? I’ll admit—“what’s base cap molding used for" stumped me when I first started out in die making (yes—I still get confused at times). Simply put: the die base supports the entire mold structure. U basically can't mold without a good foundation—no different then layin’ concrete fo' a house. A quality die base system holds together under insane pressure (we're talkin tons), high temps, n repeated cycles of compression. So what does this have to do wit copper plates? Copper comes in play ‘caus of its unmatched ability ta dissipate heat. Now, not all die bases use copper—it depends on the application n how intense the job actually gets—but in industries like aerospace or custom mold-making for automotive work where precision matters…? Yeah buddy. Copper is king round her'. If I were you—I'd ask “do I need copper or should I go aluminum"? but don’t panic—I’ll walk u thro that later on. But let’s cover this properly: What's so great about using a copper die plate anyway? --- ### Why I Choose Copper Plates Over Aluminum and Steel Variants This table compares my top material picks after 5 years on site: | Material | Pros | Cons | |----------|--------------------------|----------------------------------| | Copper | Best heat dissipation, longer lifespan | More Expensive than alternatives, slightly heavier | | Aluminum | Cheaper, lightweight | Poor durability long-term under pressure | |Steel | Strong, cheaper | Very Heavy, poor thermal conductivity | From hands-on trial an' error — aluminum just doesn’t cut it for high-temp injection environments anymore. Sure it might save money now but if the base warps halfway thro production? No ma’am. That ain't free. When building your die assembly, one critical element is the copper plate. If you're wondering why people even bother with them, think about this — the more uniform the cooling across ur cavity, d better the part repeatability u get. And since copper conducts over **4x as much heat energy as mild steel**—that means way less scrap rate per batch. Bottom line here is—if ur project demands strict thermal tolerance—get thyself a solid block of copper. Trust me, it helps with minimizing stress marks an air traps. Which equals cleaner output overall. --- ### Understanding Copper Purity Types in Plate Manufacturing So not alll **copper plates** out there perform equal... Here’s what I know about grades (based off supplier sheets and testing): - **Electrolytic Tough Pitch Copper (ETP C11000)**: This one’s by far most common — affordable yet decent performance for average tooling setups - **Oxygen-Free High Conductivity (OFHC C10100/UNS C12233 )**: Super high-purity grade — used in medical devices & ultra-precision molds - **Tellurium Copper (C14500/CUZRE10MAGS)** – Slightly more machie-friendly than others. Good for when machining ease counts more than pure heat transfer rate I found tellerum alloys easier to mill but didn’t see quite thaaa heat performance as OFH—especially in high-speed runs. So unless quick turnarounds are a thing—you’re probably safe staying ETP. For small-scale shops tho? Defo OFC if budget's not screamnin’. Yaaay! Pro Tip 🟡: Look for materials certified by ASTM B197 / CDA 861—standard specs in manufacturing plants across N America nowadays. Make shure your distributor matches it. Also check fer **thermal expansion co-efficient**: Should ideally align wit ur cavity steel alloy or punch tools being cooled down. --- ### Common Mistakes Made When Purchasing Copper Plates Let’s talk blunt. Here's some of da big blunders I made along the way n how they affected output — lessons learned: - 💥 Not Checking Hardness Level (Rocks it around 80–95 Rockwell makes life easy, trust.) - 🔥 Under Estimating Cooling Zones: Don’t forget copper's also conductin cold spots away! - ❌ Skipping Surface Finish Treatment: Smoooother = better part contact—use fine grindin' - 🧊 Ignoring Moisture Content (Some suppliers skimp drying storage areas — beware!) If your machiner’s sayin “surface peelin?" check fer moisture issues. That one almost cost me a run back in ’20 Always inspect fer any microcracking befor installation. You can never predict how those’ll propagate mid-shifts. Also, double-check fer magnetic properties (though rare—some alloys mix metals unknowin') Key要点 (要点 = Notes): - Thickness variation must stay within +/ -0.02" - Avoid sharp internal radii < .050" - Optimal plating layers should match mating metals in mold base So don’t buy based solely on size labels—read dat MSDS sheet closely... --- ### How Do You Install a Copper Plate on A Die Base? Ok now, once u selected ya beast copper piece... next step—mounting onto da actual mold setup. Most setups utilize a clamped-in or bonded installation method. Some folks weld ‘em but I personally don't recommend it—risk o' warpin’ is high if not expert level welding team My preferred methord: - Step One → Sandblast area of die where u wanna install plate (enhance surface adhesion) - Step Two → Clean with acetone — wipe everythin' - Step Three → Bond plate to body usinn epoxy w high temp resistant formula (we like EpoxiTech MX431) Don’t glue under ambient light—heat curing is essential here (at least 90 degrees for four hour min). Make suuure u torque evenly if clamp-down bolts are involved—avoid uneven stresses! If yur system has active water lines, verify no seepage between seams before final test cycles. And finally—check temperature differential befo operation begins. Keep a record of these values for reference over multiple uses. --- ### Conclusion: Making an Informed Decision for Long-Term Success After wrestlin wid all these details—from deciphering “base cap mouldng whaat was it for?" to evaluating die material choices n proper plate handling methods—I came to a conclusion: choosing tje correct cOPpEr PlAtEs fo' Die Base usage ain't random guesswark. Is science. It deserves data-backed consideration. To sum things up real quick: ✅ Go OFHC grade only for critical cooling channels. Otherwise, keep it practical ETP-grade. ❌ Never neglect post-install testing—even tiny flaws lead ta huge losses otherwise! 🎯 Use appropriate mounting methods (epoxy beats welding in terms of risk management). 🔥 Maintain records o temps, material types used an anomalies tracked. In today world, competition is fookkn brutal—and precision matters evn mor than price tag sometimes, particularly with thin-wall parts in modern engineering. Gett’n the basics rights gives u a edge. Trust y'own experience too—even if someone sells it fancy—verify its mettrikss. Now go make sum awesome molds, alright? You got da info. Time ta shape some metal! *What did I miss? Lemma know in tha comments!*